Vinyl mastering is essential for transferring your music to a record. It addresses specific challenges such as frequency response, phase and dynamic range. It also engraves the sound onto a disc to play well on a turntable.
Not all recordings are equal or sound good on a disc, which is why you need a mastering engineer. Professional mastering can elevate your album and strengthen its impact, whereas mastering that does not respect the format might downgrade the quality.
While the importance of hiring a professional mastering engineer is undeniable, on this page, we’ve compiled a brief guide about audio preparation for vinyl cutting. Here you will find tips for better mastering, album sequencing and vinyl length. Follow these guidelines to ensure your album sounds its best on vinyl.
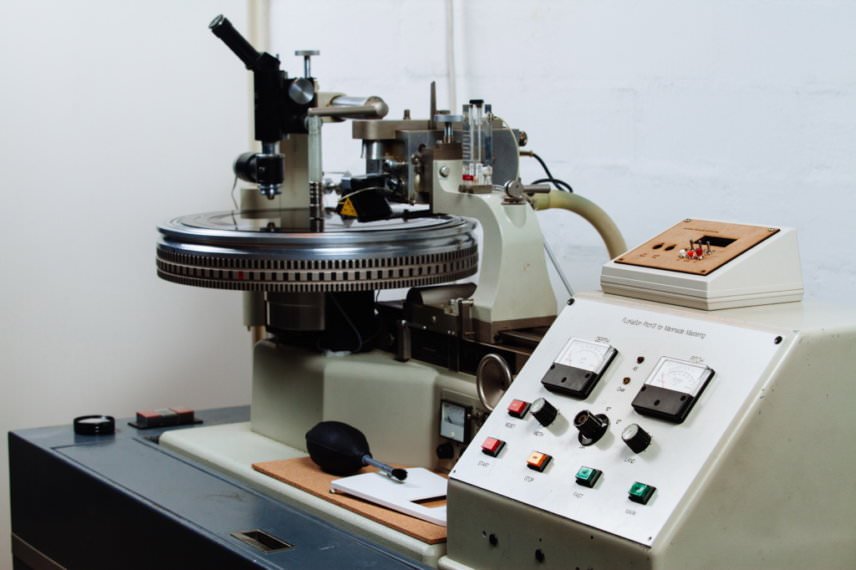
Vinyl Mastering Checklist
When mastering for vinyl, a key task is adapting the digital sound to the analog format of a record. Here is a basic checklist designed to address the limitations of vinyl and help prevent technical issues in the cutting room.
Peak Level
- Keep peak levels below 0 dB to prevent digital clipping and distortion.
- Use limiting wisely to preserve natural dynamics while preventing distortion of the loudest peaks.
Bass Frequencies
- Apply a high-pass filter to cut all frequencies below 20 Hz to reduce rumble.
- Keep low frequencies below 250 Hz in mono to ensure playback stability and a balanced low end.
High Frequencies
- Avoid excessive peaking above 15 kHz to prevent distortion.
- Use de-essing to smooth harsh sibilance, especially from vocals.
Phase and Stereo
- Avoid negative phase returns to ensure all elements are phase-coherent.
- Keep stereo width between +0.5 and 1 to prevent playback issues and maintain a stable sound image.
Dynamic Range
- Use light compression to elevate quiet sections above -60 db, the vinyl noise floor.
- Ensure clarity in softer passages to avoid masking them with surface noise.
File Formatting
- Export files in lossless formats like WAV or AIFF.
- Use a resolution of 24-bit with a sample rate of 44.1 kHz or 48 kHz.
Tips For Better Mastering
Mastering for vinyl requires careful adjustments to ensure your music translates well to the format’s physical limitations. Factors like dynamic range, stereo width, and high-frequency response all impact how a record will sound on a turntable. The following tips address key areas where mastering choices can affect playback quality, helping to prevent distortion, tracking issues, and unwanted artifacts while maintaining the integrity of your mix.
Compression and Limiting
Compression helps control dynamics, but excessive use can remove the music’s energy and reduce clarity. Apply light compression to smooth peaks without flattening the sound. The limiters should only be used to tame transients, not to maximize loudness. Over-limiting can lead to groove distortion, especially on louder sections.
Use EQ to enhance perceived loudness by emphasizing midrange clarity rather than pushing a limiter. This keeps dynamics intact while improving presence.
Noise Floor and Dynamic Range
A very wide dynamic range can cause issues on vinyl. If quiet parts are too low, they can be masked by the noise floor. If boosted too much, the louder sections may distort. Use upward compression to lift quieter parts while leaving loud sections unchanged. This keeps soft details audible without increasing distortion risks. Sudden jumps from very quiet to very loud can strain the cutting process, creating tracking issues and echoes.
Sibilance Distortion
Excessive sibilance in the 8–10 kHz range will exaggerate on vinyl, leading to distortion. A dynamic EQ is an effective tool to reduce sibilance only when needed, without dulling the mix. Not all needles track high frequencies the same way. Aggressive sibilance may sound different depending on the playback system.
High-frequency response diminishes toward the inner grooves due to lower groove velocity. Additional de-essing or attenuation in the upper register may be needed as the needle moves inward to help maintain consistent playback.
High frequencies above 15 kHz demand rapid groove movement, which cause distortion or tracking issues on certain turntables. Apply a gentle filter roll off from 15khz to ensure compatibility across a range of playback systems.
Stereo Low-End
Wide grooves from stereo bass limit the available space on a record, requiring quieter overall levels.It may force the needle to move unpredictably, leading to distortion or even skipping. At the very least, low-end energy in stereo can create phase inconsistencies, making the groove harder to track. Keeping low end in mono and striking the right tonal balance allows for longer and louder albums.
To achieve this, use an elliptical EQ to progressively narrow bass frequencies below 150–250 Hz, ensuring a more stable and trackable groove.
Vinyl Length and Sequencing
By managing side lengths and sequencing strategically, you ensure that your record plays back with the best possible sound quality, preserving the impact of your recording in the vinyl format. To mitigate the negative effects of a disc, please take note of the following:
Equal Sides: Aim to keep each side’s duration within one minute of each other. This balance ensures the best possible audio quality across both sides. Making one side much longer than the other diminishes the quality of the whole album.
Optimal Length: For optimal fidelity, keep each side below 22 minutes. Longer sides require narrower grooves, reducing level output, low-end, and high frequency reproduction. For maintaining high fidelity of the recording that exceeds 45 minutes, consider releasing over 4 sides of a double LP.
Track Sequence: Place louder, high-energy songs at the start of each side, where groove velocity is highest. Reserve quieter and less complex tracks for the center to minimize distortion and high-frequency loss. This approach promotes optimal clarity and fidelity across the entire album.
Vinyl Playing Time Per Side
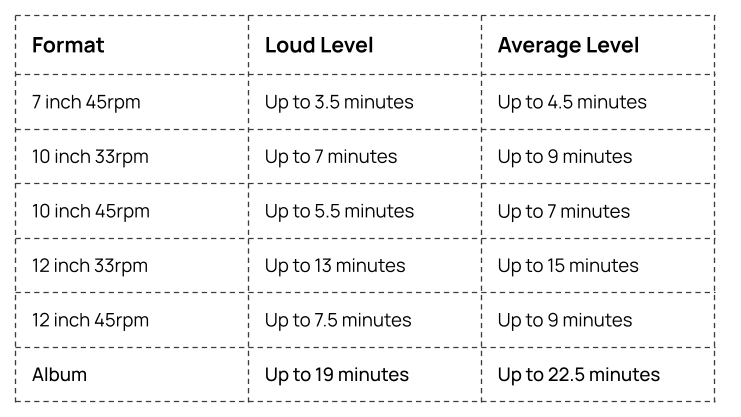
Lacquer and DMM
Vinyl mastering is done using either lacquer cutting or Direct Metal Mastering (DMM), where music is engraved onto a 14-inch master disc. This disc is then processed and plated with silver and nickel to create a negative stamper for pressing records.
With us, you can choose between lacquer or DMM cutting. If you haven’t specified a preference, we will select the most suitable method based on our expertise to ensure the best possible sound quality. Below, you’ll find a brief introduction outlining the advantages of each method.
Lacquer Cutting
Lacquer provides a warm, rich sound, making it a popular choice for genres that benefit from a fuller low-end, such as jazz, rock, or electronic music. It allows for greater lateral groove movement, preserving a wider stereo image and a more spacious soundstage. The softer material enables smooth high-frequency transitions, reducing the potential for excessive sharpness.
However, due to its softer composition and additional chemical processing, lacquer may produce a higher noise floor. It is also more susceptible to pre-echo, where groove modulations create faint imprints of loud transients before they occur. Despite these drawbacks, lacquer cutting remains widely used for its balanced tonal characteristics and classic vinyl warmth.
Direct Metal Mastering
Direct Metal Mastering (DMM) offers a cleaner high-frequency response, reduced distortion, and lower surface noise compared to lacquer. That makes it ideal for music that benefits from precision and clarity. The process eliminates pre-echo effects and allows for tighter groove spacing, which can accommodate longer playing times. However, DMM’s tighter groove structure can lead to a slightly narrower stereo image, particularly in the low frequencies, as bass is often summed to mono more aggressively.
DMM is also known for its distinctively bright and highly detailed top end, which makes transients and high-frequency elements—such as cymbals, strings, and vocals—sound crisp and articulate. This can enhance certain genres, particularly those with intricate arrangements or acoustic textures, but may also feel less smooth compared to lacquer’s softer, more rounded presentation.
Vinyl Record Production Stages
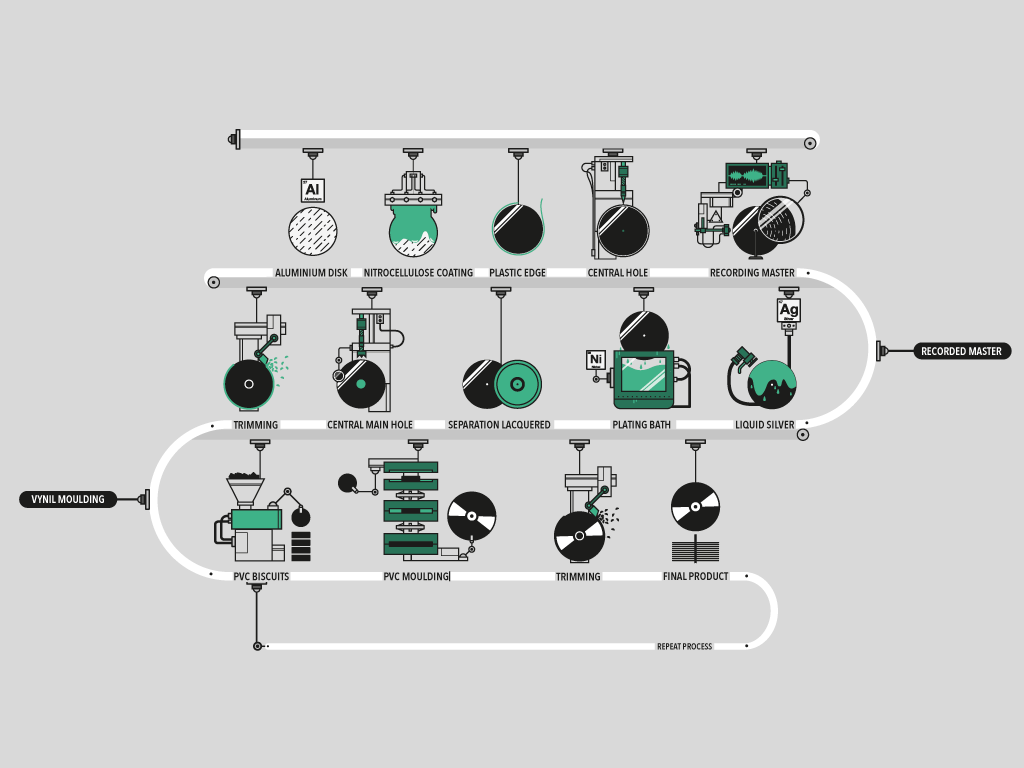
Choosing the Right Speed
Playback speed affects sound quality, playtime, and how audio is cut onto a record. The two standard speeds—33 ⅓ RPM and 45 RPM—serve different purposes. In most cases, playtime determines the speed, but if you have a choice, here’s how they compare.
33 ⅓ RPM is the standard for LPs, allowing for longer playback per side by using tighter groove spacing. However, as the disc fills up, grooves become more compressed, reducing dynamic range and high-frequency clarity. The slower stylus movement also results in softer transient detail, making the overall sound less crisp than a 45 RPM pressing.
45 RPM is preferred for singles, EPs, and high-fidelity pressings due to its faster stylus velocity. Which allows for wider grooves, better dynamic range, and clearer high frequencies. Since the needle tracks more groove length per second, 45 RPM delivers greater precision, making it ideal for music that demands loudness, accuracy, and clarity.
7-inch records are mostly cut at 45 RPM to counteract distortion and preserve high-frequency clarity in the inner diameter.
Half Speed Mastering
We can master your album at half speed which may improve fidelity, clarity, and stereo imaging. This is achieved by running both the audio source and cutting lathe at half speed to engrave finer groove details, particularly in high frequencies.
A precise groove geometry reduces distortion and sibilance while enhancing transient response and stereo depth. Half speed mastering may benefit detailed music such as jazz, classical, vocal or acoustic recordings. But it is not always necessary and the difference may be less noticeable on bass heavy or compressed material.
Reference Disc
With us, you can start confidently with a reference disc, which is a one-off lacquer or DMM cut made in real time. Unlike a test pressing, which is made from a stamper, a reference cut allows you to check how the master translates to vinyl without committing to a full pressing run.
Reference discs are useful for evaluating tonal balance, groove tracking, bass response, and high-frequency detail on a turntable. They help catch potential issues like sibilance, distortion and phase before finalizing the master. Since vinyl has unique playback characteristics, a reference disc helps to evaluate how the cut works on different playback systems.
While not mandatory, a reference disc is recommended for complex mixes, dynamic material, or critical high-fidelity releases where precision is key. It is also highly beneficial for first-time vinyl makers as it provides an opportunity to approve the sound before moving forward with plating and full-scale production.